DRY MAGNETIC SEPARATION TECHNOLOGY FOR THE …
In universities and research institutes, the technique used for efficient recycling of iron mainly include dry magnetic separation of bulk slag, wet stage grinding and magnetic separation, wet …
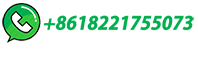
In universities and research institutes, the technique used for efficient recycling of iron mainly include dry magnetic separation of bulk slag, wet stage grinding and magnetic separation, wet …
Methods of separating residual carbon from CGFS include screening, gravity separation, froth flotation, and chemical treatment [1], [8].Among them, as a commonly used fine-grained separate method, froth flotation has been widely noticed in CGFS separation due to its advantages of low cost and good generalizability [9].However, large collector dosage and …
(a) Process flow sheet for the recovery of rare earths from rare-earth molten salt electrolytic slag by magnetic separation–sulfuric acid leaching–water leaching–HF cycle precipitation; characteristics of the main phases in magnetic fraction: (b) magnetite and metallic iron are produced as separate phases, (c) a small amount of rare ...
The flow chart of direct reduction of non-ferrous smelting slag—magnetic separation (Gao et al., 2022). Zhao et al., 2016a, Zhao et al., 2016b utilized the Eqilib module in FactSage for theoretical calculations of the carbothermal reduction process.
To make clear the interaction of the separator structural parts, let us consider the separation process. When conveyer belt 1 moves in the direction of the arrow the separated slag goes …
Minerals in titania-rich slag ordered by decreasing mass densities Mineral species Classification according to mineral density Iron Highly dense minerals fraction ... Among other techniques, the magnetic separation was the most efficient, especially when performed on ground titania-rich slags (Gue´guin 1972, 2004a). The separation was based on ...
High iron bauxite (IRB), red mud (RM), and fly ash (FA) are resources rich in iron and alumina, yet there are no effective methods of recovering and utilizing them. In this paper, a new reduction smelting technology for the extraction of iron and alumina from IRB, RM, and FA is proposed based on the technology platform of "Slag Metallurgy, Mineral Recycling, and …
Slags coming from stainless steel (SS) and ferrochromium (FeCr) production generally contain between 1 and 10% Cr, mostly present in entrapped metallic particles (Fe–Cr alloys) and in spinel structures. To recover Cr from these slags, magnetic and gravity separation techniques were tested for up-concentrating Cr in a fraction for further processing. In case of …
Copper slag is a byproduct in the copper smelting process, rich in Pb, Zn and Fe and is an important recyclable secondary resource. In this study, Pb, Zn and Fe in copper slag were successfully recovered by the novel process of salt roasting-magnetization roasting-magnetic separation.
After reduction at 1280 °C for 35 min, they subjected the material to magnetic separation, resulting in iron concentrate with an iron grade of 90.35%. The iron recovery rate was 89.70%, and the copper content in the iron concentrate was 0.35 wt% . The typical copper slag reduction-magnetic separation process flowchart is shown in Fig. 2. From ...
Magnetic separation has wide-ranging applications in both mineral processing and recycling industries. Nevertheless, its conventional utilization often overlooks the interplay between mineral and particle characteristics and their impact on operational conditions, ultimately influencing the efficacy of the separation process. This work describes a methodology able to …
An innovative technology for direct reduction-magnetic separation with the addition of Na 2 CO 3 and CaO was studied to upgrade copper slag assaying 40.33% Fe total and 0.65% Cu.
This results in an increase in the grade of the iron concentrate and the small portion of the metallic iron is ground too finely with the chondrites into the magnetic separation tailings. At the grinding time of 45 min, the magnetic separation iron ore concentrate exhibits improved iron grade and recovery rate (93.61% and 90.71%, respectively).
slag can be obtained in a short time through a semi-smelting reduction and magnetic separation process. The maximum particle size of iron nugget is about 15 mm, and the recovery rate of the iron
The presented work offers an innovative process scheme for valorizing Pb-Zn slag, which involves crushing, grinding, and separation techniques to concentrate valuable components (non-ferrous metals). This …
The electric arc furnace (EAF) smelting ilmenite concentrate process which produces titania slag, is high energy consumption, high pollution, and low efficiency process. An economical and clean process for semi-molten reduction followed by magnetic separation to produce titania slag from Panzhihua ilmenite concentrate is proposed. In the present study, …
The Cr present in stainless steel slag, charg e chrome slag and vanadium slag usu- ally exists as Cr 2 O 3 . However, there is a possibility that it is oxidized to hazardous
When the mixed slag was modified at 1200℃, the grade of magnetic slag by magnetic separation was 31.14% and the recovery was 64.04%, which had the potential of returning to sintering or ...
It could be considered that the slag inclusions in the magnetic separation iron and the separated slag had the same composition, so the content of the inclusive slag in the magnetic separation iron was ω inc = Ca iron %/Ca slag % = 10.6 wt%. According to the ratio of Ca and P elements in the fluorapatite gangue phase, the content of P brought ...
In order to solve the problem of solid waste pollution of basic oxygen furnace (BOF) slag in the metallurgical process, this paper took BOF slag as the research object, and carried out oxidation reconstruction of BOF slag and alcohol wet magnetic separation recovery of iron phase, so as to efficiently recover and utilize BOF slag. In the early stages, the research …
Magnetic separation is an effective method to recover iron from steel slag. However, the ultra-fine tailings generated from steel slag become a new issue for utilization. The dry separation processes generates steel slag powder, which has hydration activity and can be used as cement filler. However, wet separation processes produce steel slag mud, which has …
In this paper, the magnetic separation characteristics of inert minerals in steel slag powder under various operating parameters of fluidized dry magnetic medium magnetic …
The flowchart diagram process followed in this study. Step 1: The chemical and phase composition of BOF slag and BFS were analyzed; ... Step 5: The magnetic slag was recovered from the modified slag by wet magnetic separation. 2.1. Materials. BOF slag and BFS used (provided by the Baotou Iron and Steel Group Co., LTD., Baotou, China.) in the ...
BF slag through a hydrometallurgy technique using H 2 SO 4 as a leaching agent. The recovery investigation has also reported that the codissolution of inorganic metal oxides such as MgO,
• Metallurgically modified slag Following coarse slag processing (recovery of metal e.g. + 20 mm, crushing of the mineral components to -20 mm) by means of crush-ing, screening and sorting technologies such as handpicking, sen-sor sorting, magnetic separation and/or dry density separation, a pre-crushed slag fraction is fed into the Loesche mill.
The results of magnetic separation are shown in Table 6. The results show that the increase of water content adversely affects magnetic separation, as the grade of the magnetic product drops from 0.98 % to 0.72 % Ni; the corresponding yield reduces from 25.82 % to 24.76 %, and the recovery reduces significantly from 81 % to 66.5 %. Table 6.
the magnetic separation process was carried out. When the iron and copper grades in the magnetic concentrate were 90.21% Fe and 0.4% Cu, 91.34% iron and 83.41% copper were recovered, respec-
Flow chart of the rotary kiln coal-based direct reduction process (Yi et al., 2022). ... A novel process to upgrade the copper slag by direct reduction-magnetic separation with the addition of Na2CO3 and CaO. Powder Technol., 347 (2019), pp. 159-169, 10.1016/j.powtec.2019.02.046.
In the stage of magnetic separation, the iron grade of the magnetic separation concentrate and the iron recovery in the gold extraction tailings were 60.9% and 74.6%, respectively. The composition of magnetic separation concentrate was determined according to the national standard of iron ore concentrate ( GB/T 36704-2018, 2018 ), as shown in ...
In this work we studied the wet magnetic separation on a very fine FS, LS and DeS slag fraction (<0.045 mm). The chemical composition of the obtained magnetic and non-magnetic fractions …
حقوق النشر © 2024.Artom كل الحقوق محفوظة.خريطة الموقع