The Complete Guide to Primary Crushing, Secondary …
11.19.2 Crushed Stone Processing and Pulverized …
Quarried stone normally is delivered to the processing plant by truck and is dumped into a bin. A feeder is used as illustrated in Figure 11.19.2-1. The feeder or screens separate large …
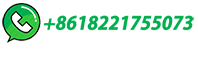